Like innenfor inngangen til Haugaland Næringspark har Ølen Betongs nye signalbygg reist seg. Og det som ser majestetisk ut fra utsiden, er ikke mindre imponerende inni. Her er det benyttet betong i alle tenkelige varianter, og fokuset på effektiv og fornybar energiteknologi gir store fordeler.
– Vi lot oss inspirere av bygg med god miljørating, gjorde det mer betongpreget og tilpasset det våre behov. På taket har vi solcellepaneler som faktisk vil dekke 85% av byggets årlige strømbehov. Vi forventer totalt å produsere 106 000 kWh i året helt selv, noe som gir store besparelser på strømregningen I tillegg har vi seks energibrønner under bakken som styrer gulvvarmen i hallene og kjølingen i hele bygget, og vi har en 30 000 liters akkumuleringstank som samle vann på eiendommen og regnvann fra taket. Dette vil bli brukt i vaskeanlegget vårt, forteller Svein Atle Berge, daglig leder i Nordic Concrete Group – eierselskapet til Ølen Betong.
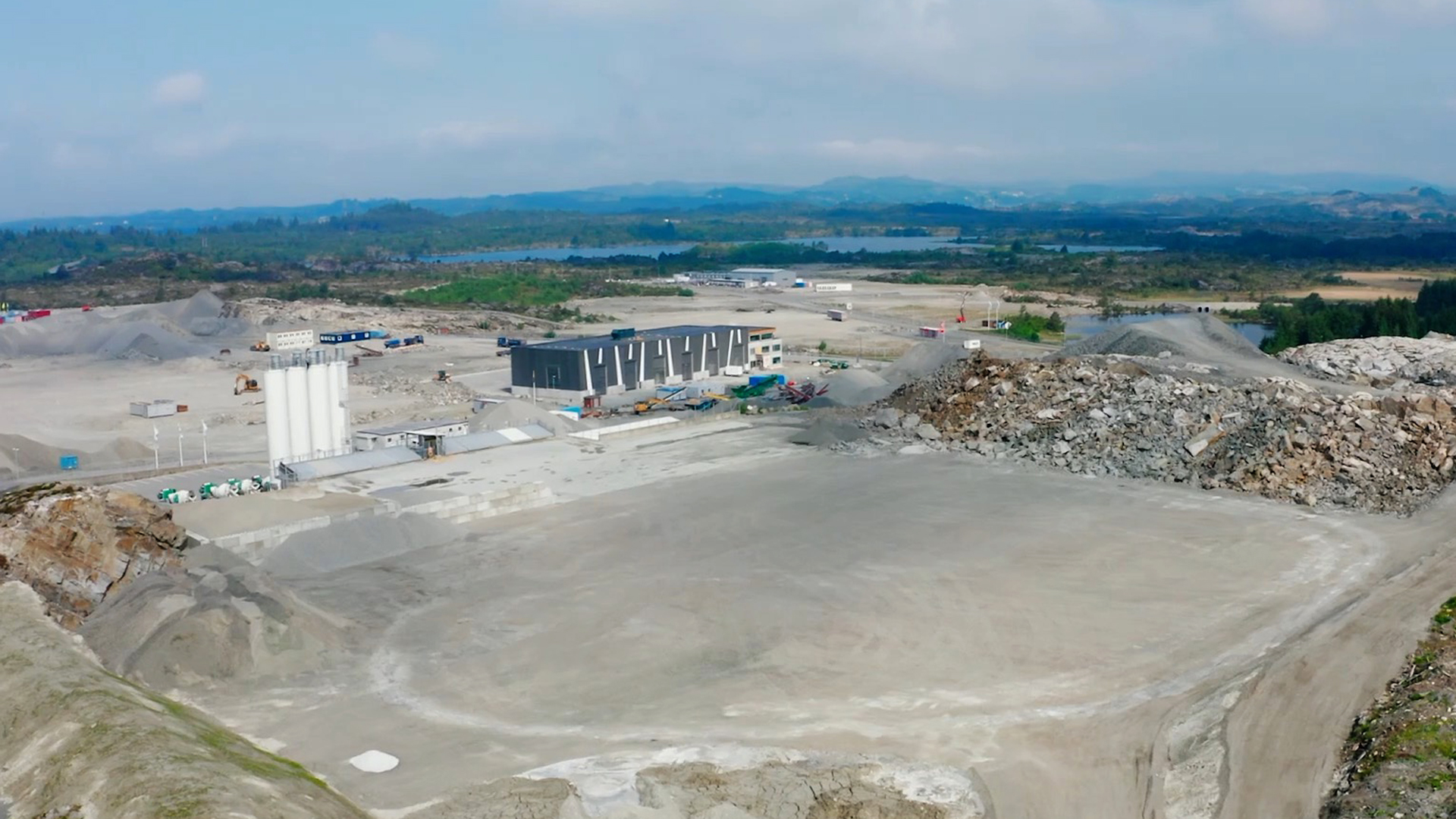
Bygget er energimerket med klasse grønn A, og de ulike energiløsningene skaper synergier gjennom en felles energisentral. Konsernet som Ølen Betong er med i har 63 ulike produksjonsenheter rundt om i landet, og satsingen på solcelle-energi i Haugaland Næringspark oppleves som et interessant prosjekt.
– Jeg må jo innrømme at det var ekstra stilig å få første faktura fra Haugaland Kraft, med egen linje for kreditt på. Særlig når strømmen har blitt så dyr som i dag. Det blir spennende å følge dette framover og kanskje kan vi gjøre dette flere steder, sier Berge.
Næringsparken har flere lokasjonsfordeler
Ølen Betong var første selskap som kjøpte tomt i Haugaland Næringspark, og har vært der siden 2012.
– Vi trengte nytt blandeverk, og så næringsparken som en ideell lokasjon med kommende T-forbindelse og inngang til Rogfast. Etterhvert har vi også kjøpt flere tomter i parken, og dermed fått god tilgang på stein som er en ressurs i produksjonen. Vi hadde behov for nytt bilverksted, økt produksjonskapasitet for spesialprodukter og administrasjonsbygg. I tillegg er utsalgslageret for vann og avløpsprodukter flyttet i fra Haugesund til Gismarvik. Tomten i Ølen er sprengt, og på Gismarvik fikk vi jomfruelig mark å boltre oss på. Da har vi kunnet bygge så stort vi har ønsket. Det har gjort at vi kan både øke produksjonen, og også samle flere andre aktiviteter på én adresse, forklarer Berge.
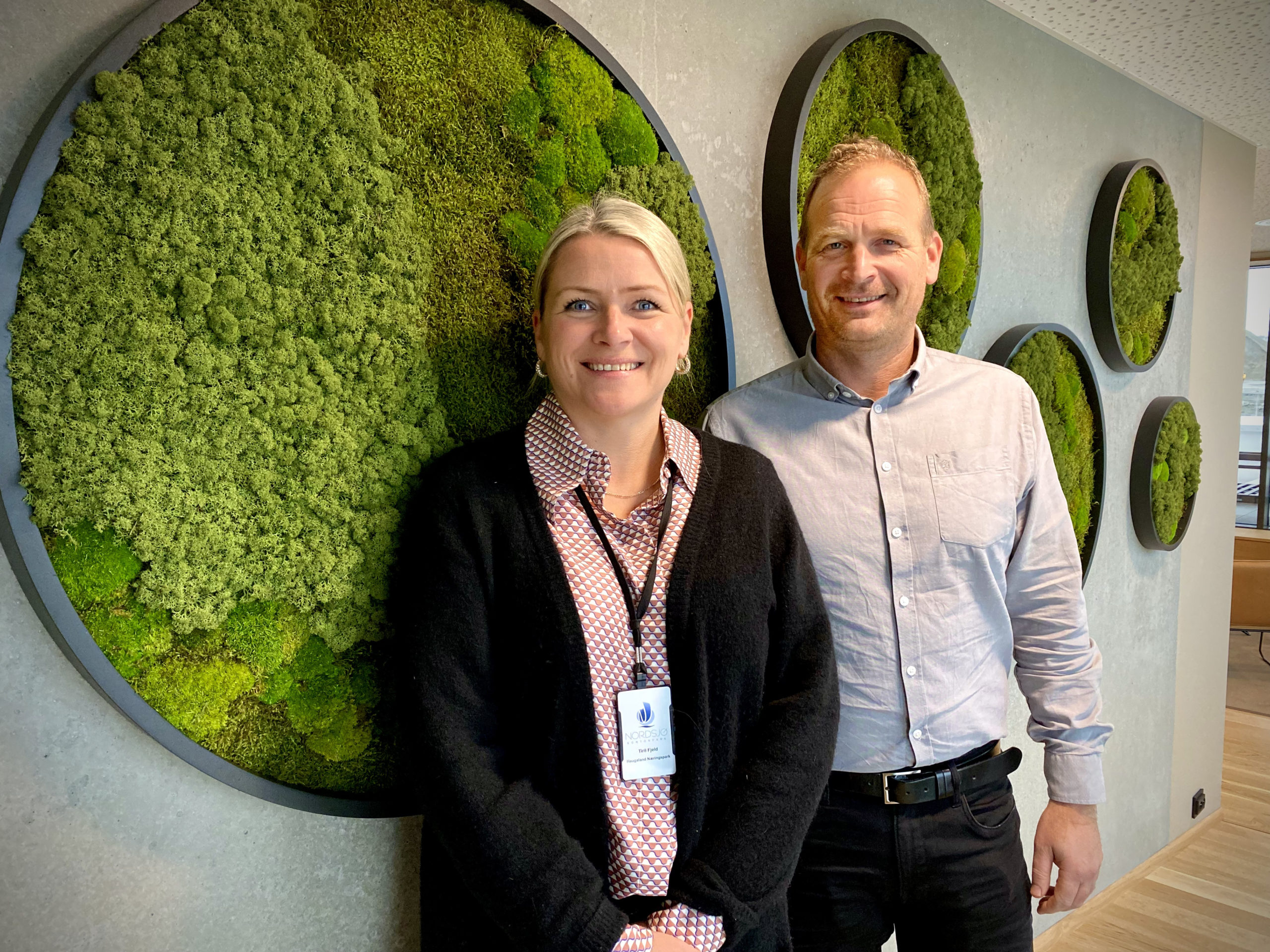
Litt av tanken med å utvide virksomhetene i Haugaland Næringspark, har også vært å komme nærmere regionsenteret.
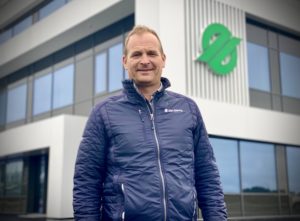
– Det er viktig for oss å være attraktive i arbeidsmarkedet, og tilfanget er naturlig nok større i Tysvær, Haugesund og Karmøy enn hjemme i Ølensvåg. Med beliggenhet med inngangen til Rogfast vil vi også være nærmere Stavanger om få år. Plasseringen gjør også det nye administrasjonsbygget til et naturlig møtested, både med kunder og samarbeidspartnere utenfra som da får kort vei fra flyplassen, og til andre typer samlinger. Her kan vi ta imot besøk, holde kurs og ha sosiale tilstelninger – med kort vei for alle. Vi tenker at bygget gir oss mange gode muligheter for vekst og utvikling, sier Berge.
Kortreiste betongvarer
Næringsparkens sentrale plassering med eget havneanlegg, gir også effektiv logistikk, som bidrar til god og bærekraftig transport av råstoff og varer. At Ølen Betong har rikelig med stein på egen tomt forenkler distribusjonen, og muliggjør kortreiste leveranser både i selve parken og til regionen rundt. Det vil kunne bety mye for både økonomi- og miljøregnskapet til aktører som skal etablere seg i Norges største industripark.
– Vi har nok stein her i 10-15 år til, og med den årsproduksjonen vi har nå, så sparer vi nok årlig 50 båtlaster fra Ryfylket, mener Berge.
Teststasjon skal sikre økt bærekraft
I 2020 fikk Ølen Betong Klimaprisen for sitt fokus på avfallshåndtering og gjenbruk.
– Asfalt har kommet langt når det kommer til gjenbruk, og vi må få til det samme på betong. Gjennom prosjektet Grønn betong har vi sett på løsninger for dette, og har nå satt av 10 mål i Haugaland Næringspark til en egen teststasjon for håndtering av slam og fremtidens gjenbruk av betongrester. Målet må være god sirkulærøkonomi der så mye som mulig kan gå tilbake i produksjonen. Tanken er å samle inn rester og overskuddsmaterial fra egne produksjonsenheter i regionen og bruke det på nytt her, sier Berge.
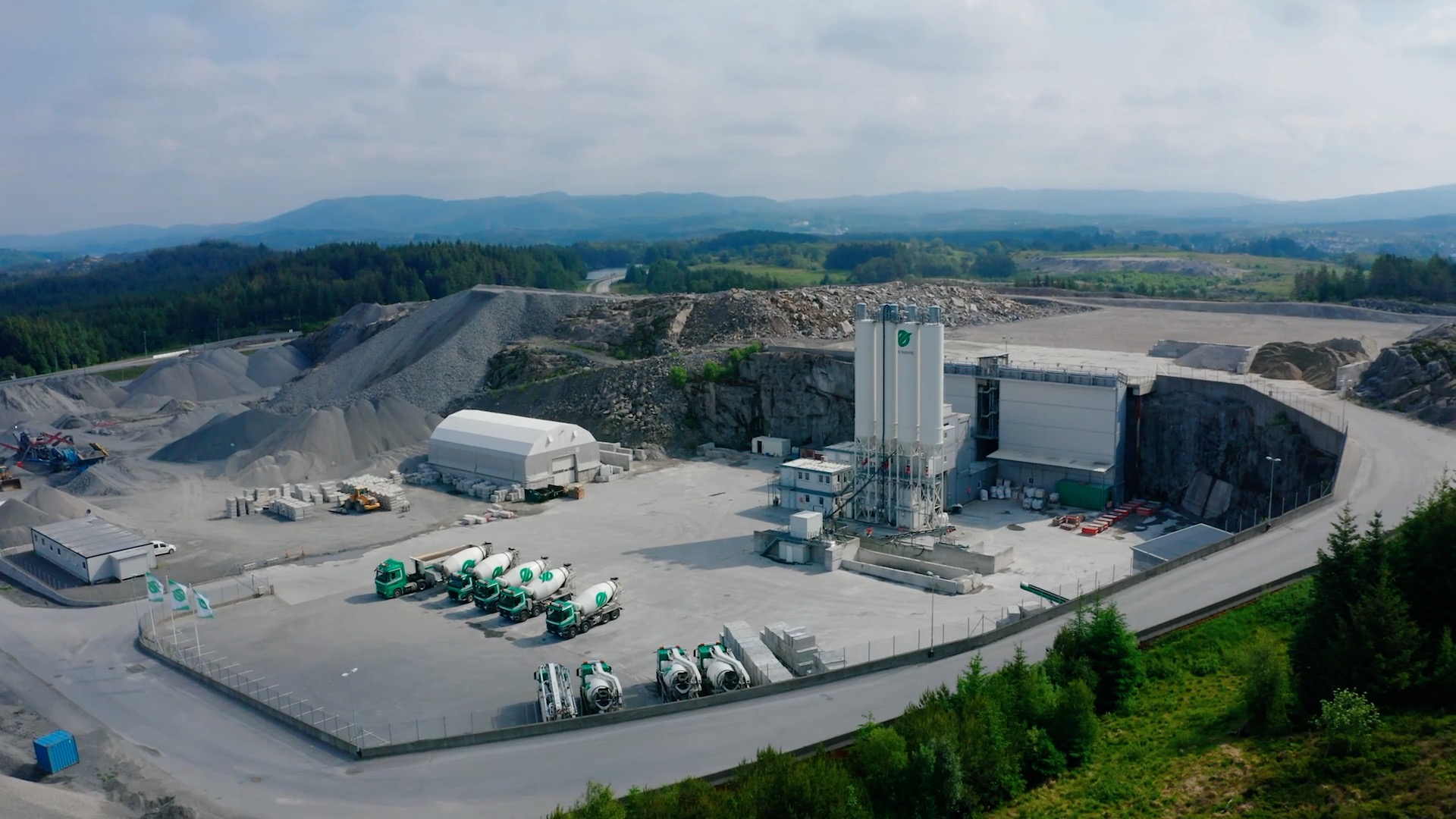
Administrasjonssenter
I 2018 slo Ølen Betong betongdelen av virksomheten sin sammen med Kongsvinger Betong, og etablerte Nordic Concrete Group, som er blitt en landsdekkende aktør.
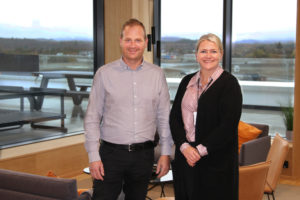
– Vi gjorde dette for å spisse aktiviteten, samle fellesfunksjoner og bli en sterk norsk aktør. Vi er store både i Stavanger og Bergen, og for oss ligger Haugaland Næringspark veldig sentralt. Totalt er vi ca 700 ansatte, driver 63 ulike fabrikker og har etablert systemer som gjør det enkelt å ekspandere.
Selskapene i Nordic Concrete Group hadde en brutto omsetning på ca 3,5 milliarder kroner i 2020.